MSA Repository "MSAR"
MSAR University's Digital Repository is a documentation and digitization of all university outcomes that are of effective value in the scientific and academic community and reflects the university's image, work, and effective contribution to society Through MSAR Digital Repository, the university managed to collect, store, archive and publish digital content - including documents, audio files, images and data sets - all in a safe place. MSAR is one of the strongest University Digital Repositories in Egypt and documented in the DSPACE community with its latest versions.
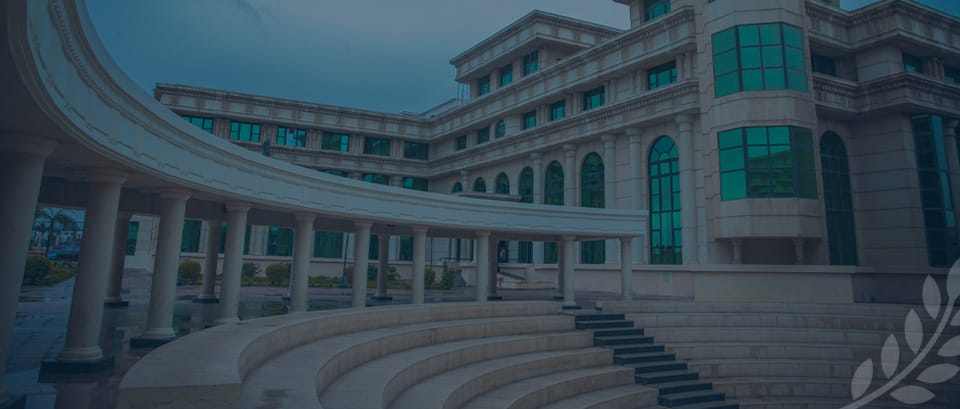
Communities in DSpace
Select a community to browse its collections.
- A Full content for MSA university Faculties Journals
- A Full content for msa university Distinguished Graduation Projects Yearbook
- Images for MSA University " sites - building - landscape "
Recent Submissions
Role of Vitamin D and Omega 3 Fatty Acids in Improving HDL Biogenesis among Multiple Sclerosis Patients via Orchestrating CHROME/APOA1-AS/ABCA1/APOA1 Milieu
(Elsevier Inc, 2025-06-16) Mai A. Abd-Elmawla; Heba R. Ghaiad; Mohammed M. Nooh; Mai A. Amer; Lobna Talaat El-Ghoneimy; Noha A. Mehana
Introduction
Clinical approaches that could correct the disturbed lipid profile may improve neurological disturbances in multiple sclerosis (MS) patients. However, the underlying mechanisms are still not well understood.
Aim
The study aimed to characterize the performance of vitamin D (Vit.D) and omega3 fatty acid (ω3) in adjusting the lipid profile of MS patients via modulating CHROME/APOA1-AS/ABCA1/APOA1 along with sphingosine kinase (SPHK)-1/2, and sphingosine 1-phosphate receptors (S1PR)-1/5.
Subjects and methods
72 MS patients were recruited for this study; 25 received Vit.D, 21 received ω3, and 26 didn’t receive any supplementation. Blood samples were collected and then plasma were separated for further biochemical and molecular investigations.
Results
Both vit.D or ω3 improved the lipid profile in the studied groups as well as elevated the expression of the lncRNA CHROME, the concentrations of ABCA1 and ApoA1 along with lowering APOA1-AS relative to MS patients without supplementation. Vit.D supplementation group revealed higher levels of SPHK1 and lower levels of SPHK2, whereas ω3 supplementation reduced both S1PR1 and S1PR5 relative to the MS control group.
Conclusion
This study demonstrated the beneficial role of Vit.D and ω3 supplementation in adjusting the lipid profile of MS patients via modulating ABCA1 and ApoA1 and their upstream regulators CHROME and APOA1-AS. The administration of Vit.D upregulated SPHK1 and downregulated SPHK2 gene expression. On the other hand, ω3 supplements downregulate S1PR1 and S1PR5 gene expression in MS patients.
Waste Reduction and Productivity Improvement in a Pack Manufacturing Company
(MSA University, 2025) Mohamad Moataz Almoriah
ALFA PACK factory is a carton manufacturing company established in 2013 to meet the growing demand for high-quality packaging. The factory is located in the 3rd Industrial Zone in 6th of October City, Egypt. The factory aims to provide packaging products that meet the needs of various industries such as food manufacturing, furniture, clothes, technology industries, etc.
After investigating the production line, three problems were observed: the first is the production doesn’t meet the customer demand because there is bottleneck in the production line. The second, 8.74% of cardboard roll is wasted during transportation of the cardboard roll by means of forklift. Third, the 30% wasted time during the setup process per shift of die-cutting and carton shaping machine.
This project aimed to increase productivity and reduce waste across the cardboard production process. To achieve this, several lean manufacturing tools were implemented, including line balancing, 5S methodology, time study, and improved roll handling systems. As a result, production capacity significantly increased particularly in the bottleneck overall productivity from 67% to 83.9% and raw material waste was reduced to 2.5%. The improvements contributed to a more stable, efficient, and cost-effective production line capable of meeting customer requirements more reliably.
These improvements led to significant financial and operational gains. The reduction in raw material waste saved the company approximately 62,000 LE per month. Enhanced productivity allowed the factory to fulfill more orders, generating an estimated 54,000 LE in additional monthly revenue. Moreover, improvements in machine setup and product quality contributed to further savings of around 3,000 LE per month. In total, the project outcomes achieved over 130,000 LE in monthly financial benefits while ensuring higher efficiency, reduced delays, and improved production stability.
Enhancing Production Efficiency in a Modern Paint Industry
(MSA University, 2025) Osama Moustafa Badr
Al-Masreya for Modern Paints (Anjo) established in 2019, is located in 10th of Ramadan City Egypt. The factory is specialized in producing a variety of paint products, including Walls Putty, Plastic Paints, Glue, and Sealers, aiming to provide competitive products in the Egyptian market. Most of their production includes Interior Putty, Exterior Putty, and Crack Fillers.
After investigating the production processes, several issues were identified. First, the Crack Fillers product consumes a significant amount of time during the packaging stage, taking up to four hours per batch, causing delays and wasted time. Second, for the Interior Putty product, the production line faces several issues that cause time waste and delays. 70% of batches require modifications due to the lack of a standardized method, which further adds time and effort. Finally, starting from batch number 2, there is a waste of time due to delays in the raw material transfer process, affecting overall productivity.
The project aims to reduce time waste in the production process by using industrial engineering techniques. To address specific issues, several improvements were planned. First, to reduce the long filling time in crack filler putty, additional scales were added to the production line to speed up the process. Second, SMED was applied to minimize machine idle time in the interior putty production. Lastly, Standard Operating Procedures (SOP) were implemented to reduce modification time in the interior putty production.
This project led to significant improvements in the production processes of Interior Putty and Crack Filler. By applying industrial engineering techniques such as SMED, SOPs, and Line Balancing, machine idle time was reduced, modification rates were lowered, and weighing operations became more efficient. As a result, daily production capacity increased by 50%, raising the number of batches from two to three per day, while monthly overtime costs were reduced by 12,536 L.E. Overall, these improvements generated a monthly profit increase of 344,360 L.E, contributing to higher productivity, better resource utilization, and measurable financial gains.
Improving Efficiency and Reducing Waste in Wood Factory
(MSA University, 2024) Aya Kasem Hamed Kasem
The Egyptian Company for Metal & Wood Industries facility specializes in producing
high end outdoor furniture. The Factory is situated in Egypt's 6th of October City's
industrial district. The factory was founded in 1986 and has since introduced a new
brand ACAJIA which is focused on producing outdoor and indoor furniture.
After investigating the outdoor furniture production line, two main problems were
observed. The first identified issue is material waste in the spindle molder machine,
which contributes to a loss ranging between 1.23% and 2.17% of the total output
across all wood cutting machines. The second issue is time waste during the manual
assembly process, particularly in the Preparation of Parts stage, which takes
approximately 2 hours, with a significant portion of this time being considered nonvalue-
adding.
The project aims to enhance productivity by reducing material waste by approximately
0.19 % to 0.20 % through the implementation of jigs and fixtures technique.
Additionally, it seeks to minimize time waste in the Preparation of Parts stage by
around 1.7 hours through the workplace redesign technique.
The implementation of the jigs and fixtures technique to address material waste in the
spindle molder machine resulted in a significant improvement, saving one full working
day per month. The total estimated savings from material reduction ranged between
1,885.6 L.E and 3,285.6 L.E per month. On the other hand, applying the Workplace
Redesign technique to improve the Preparation of Parts stage led to a time saving of
7.4 hours per month, with an associated cost saving of approximately 231 L.E.
Implementing Material Requirement Planning System in a Food Industry
(MSA University, 2024) Aya Mohamed ElSaadany
Fresh Food Factory is a member of AL-Mansour Group established in 2014 and located in industrial zone in 6th of October. Fresh Food Factory filled a gap in the market for an upscale and luxurious supermarket, leading to the creation of a niche shopping destination that offers customers a premium and unique culinary experience. Serving over 250 supermarkets, including Kheir Zaman and Metro. Fresh Food Factory offers a diverse range of handcrafted products such as butchery, poultry, bakery items, chocolates, and ice cream.
Upon investigating the food production process, significant delays in raw material availability and the failure to meet required order quantities have been identified. Inadequate forecasting techniques can result in shortages or excess raw materials, leading to ineffective process management, while poor inventory control exacerbates these issues. Consequently, deficiencies in these areas contribute to increased costs and customer dissatisfaction.
The project aims to implement a Material Requirements Planning (MRP) system to enhance planning, productivity, and order fulfillment while optimizing inventory control and reducing costs. This was achieved through the application of industrial engineering techniques, including ABC Classification, Cause-and-Effect Diagrams, DMAIC, Forecasting, and Material Requirements Planning (MRP).
Keywords: ABC Classification, Cause-and-Effect Diagrams, DMAIC, Forecasting, and Material